Freeze VacuumDry Machine-Microwave tech
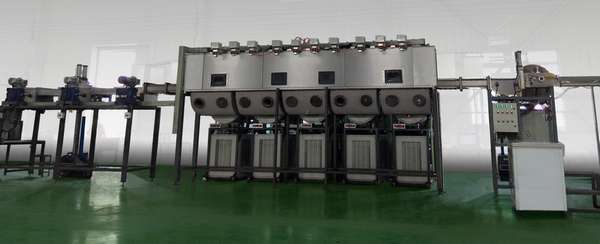
Our microwave freeze vacuum dry machine(products line) can furthest keep the raw material’s original shape,color,nutrient and aroma and its quality is better than that ones using the traditional freeze dying method.
Production parameter:
Type | D-MFD-20 | D-MFD-50 | D-MFD-100 | D-MFD-Y50 |
Power For Microwave | 22KW | 65KW | 110KW | 54KW |
Power For Vacuum System | 20KW | 55KW | 85KW | 53KW |
Power For Cold Trap | 25KW | 70KW | 120KW | 66KW |
Maximum Moisture Content of Raw Material | ≤95% |
Moisture content of Products | ≤5% |
Yield | ≥95% |
Unit dehydration capacity | 20kg/h | 60kg/h | 100kg/h | 70kg/h |
Operation Staff | 8 | 8 | 10 | 8 |
Area | 100m2 | 200m2 | 400m2 | 200m2 |
Microwave leakage | ≤5.0mW/cm2 |
Below is some freeze dry products using our freeze drying machine to be deal with .
Technological advantage:
1.Efficiency advantage
When using freeze drying,the material need heat for sublimation.Usually the methods of heating is electric heating, fuel heating, heating alcohol,but with the shortcoming-too long heating time & too large energy consumption.
In a certain vacuum state,there is almost non convection current,can only rely on conduction method to add sublimation heat to the material, so the drying time is very long, very slow.Energy consumption and processing costs is high.But if using microwave,it can heat the material inside and outside at the same time.Using our microwave continuous freeze-drying production line to dry the materials, its speed and performance is 4-20 times than the conventional heating method.
Below is an example:
| Cut Tobacco
| Cabo | Potato | Rice |
Original Water Content (%) | 60 | 50 | 80 | 70 |
Thickness (mm) | 40 | 40 | 40 | 40 |
Water Content At Last | 5 | 5 | 5 | 5 |
Freeze Drying Time | 120 | 120 | 90 | 90 |
2.Quality advantage
When microwave is used for freeze drying, the drying process has no sensible heat.With microwave freeze drying ,the material can keep the original shape, color, nutrient and aroma.What’s more ,the product quality is better than the traditional freeze-drying method.
3.Cost advantage
Microwave energy can almost 100% do effect on the material,so energy saving is very large.Now our machine make the continous production to be realized which can save the cost of labor.
System Composition:
1.Composite microwave freeze-drying warehouse
The below ,left and right of the warehouse is made of non-metallic wave material.The composite microwave freeze-drying warehouse has a good vacuum sealing performance,and it can prevent the glow discharge of microwave happenning in the vacuum condition which ensure the freeze drying enviroment not to be damaged.

2.Low temperature system
Low temperature system is mainly composed of two parts, one is cold trap, another is cold storage. The cold trap is connected to a vacuum and a freeze-drying tank for trapping evaporative water vapor.The cold storage is used to freeze the material below the eutectic point.
● Cold trap, cold storage can adjust the freezing temperature, for different materials to choose a different freezing temperature to achieve maximum energy savings.
● Cold trap, cold storage’s insulation is perfect which minimize the loss of cold.
● All accessories are provided by manufactures with famous brand to ensure good, high stability, more energy efficient.

3. Vacuum system
• The vacuum pump is connected to the cold trap through a vacuum pipe to provide a reliable power for the condensation of water vapor in the system.
● Reducing equipment costs and operating costs by using of the rotary vane vacuum pump and Roots pump combinationally to creat vacuum.
● The composite microwave eliminator is adopted to solve the microwave leakage problem of material inlet and outlet. The authority of the department measured the leakage energy of the device,the value of microwave leakage is much lower than the GB 5.0Mw / cm2.
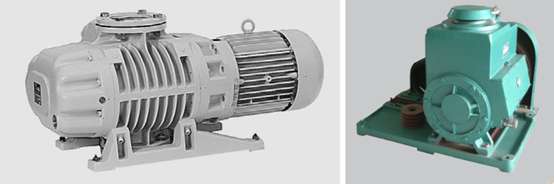
4. Control system
● Advanced electrical engineer design, selection of high-quality accessories and wires from famous brand manufacturers, wiring beautiful, high reliability,Siemens automation equipment ensuring good stability, touch screen with beautiful interface and easy to learn.
● In the whole freeze-drying system, the inlet and outlet chamber adopts the rapid decompression buffer continuous feeding and discharging mechanism, so that the whole freeze-drying process is continuous and fast. In the discharge side with frozen material moisture monitoring, both to determine the end of freeze-dried or freeze-dried end of the feedback control.

Related Items